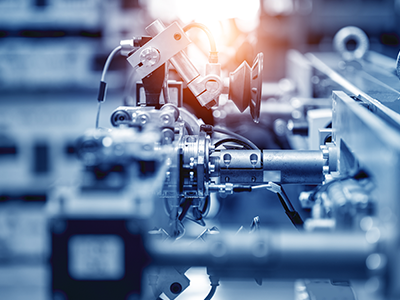
トヨタグループで設備投資が止まった?
ゴールデンウィーク明け以降、トヨタグループの設備投資にブレーキがかかっている、という話をよくききます。具体的には完成車メーカーやティア1など、いわゆる大手が設備投資を止めていて、逆にティア2やティア3など実際に部品の量産を担っている様な会社は好調だといいます。
その要因はやはり、内燃機関からEVシフトへの影響といわれます。
例えば今年、アイシン精機とアイシンAWが統合して、アイシンという新会社が発足しました。同社の主要商品はオートマチックトランスミッションです。オートマチックトランスミッションはAT社に欠かせない重要部品であり、独自技術が求められエンジンよりも単価の高い部品です。従って差別化されていて、その結果収益性の高い部品であるといえます。
しかしESGという時流の中で、同社としてはモーターと減速機を組み込んだeアスクルというEVの部品を全面的に訴求していますが、前述のオートマチックトランスミッションほど差別化された部品ではありません。
逆にオートマチックトランスミッションの開発は、同社の子会社であるシーヴイテックという会社に移管するそうで、内燃機関の主要部品の開発を別会社に移管するという動きはここにきてかなり一般的な動きになってきていますが、こうした状況ではレイヤー上位の会社ほど設備投資の判断は難しくなります。
あくまで個人的見解ですが、内燃機関からEVシフトへの過渡期の中で、設備投資の判断を「様子見」している結果、設備投資にブレーキがかかるという現象が起きている可能性があります。
中国より安い日本の部品加工
逆に、今まででは見られなかった様な新たな引合いも発生しています。
例えば私の顧問先の某部品加工会社(従業員30名)は、かねてからデジタルマーケティングに取組んでいましたが、先日、同社のWebサイト経由で問い合わせがきた大手製鉄会社から、わずか10日間ほどで新規取引口座を開設することができました。
その某部品加工会社は大物プレート加工が得意な会社なのですが、その大手製鉄会社の担当エンジニアの方いわく、「中国の外注先よりも安かった」「それなら国内の方がよい」との話でした。
今、国際的に物流価格が値上がりしています。その結果、特に大物ワークになればなるほど物流費が上がるという現象が起きています。その結果、以前であれば中国の方が安かった品物が、物流費やリードタイムまで加味すれば日本国内の方が安い、という現象が起き始めています。
これはある種のチャンスともいえるでしょう。
「工場見学無し」で、大手製鉄会社が新規口座開設をしてくれた理由
さらに興味深い現象が発生しています。
前述の新規口座を開設してくれた大手製鉄会社は、一度もその部品加工会社を訪れたことがありません。
通常、新規取引の際には必ず発注先の工場を見学した上で、取引の可否を判断するものです。ところがその大手製鉄会社の担当エンジニアの方は、「いえ、特に工場見学とかは結構です」「この書類に必要事項を記入して捺印してもらったら口座を開設しますよ」と、いうのです。
「なぜですか?」と聞くと、「御社のYoutubeチャンネルを観ました」
との回答でした。
ちなみに、この部品加工会社は1年前からYoutubeチャンネルを開設しました。
同社のYoutubeチャンネルのコンセプトは「バーチャル工場見学」で、同社の全設備など40を超える動画をアップしています。いずれの動画もお手伝いさせていただいている、船井総合研究所の若手コンサルタントがスマートフォンで撮影した動画を編集したものです。
一昔前、会社案内動画をつくるとなると、一声100~150万円が相場でした。
しかし今はそういう時代ではありません。一筆入魂の高価な動画を1つつくるのではなく、スマートフォンで良いので多数の動画を撮影して数多くアップするのがYoutube時代の動画マーケティングのあり方です。
そして今や、大手企業のエンジニアも、サプライヤー選定の際にYoutube動画は必ず参考にしています。特に製造業の場合は、必ず自社のYoutubeチャンネルを立ち上げるべきでしょう。
日本の製造業が目指すべき方向性とは?
さて、冒頭にも述べた通り製造業のマーケットの大半を占める自動車マーケットが、これから内燃機関からEVへとシフトしていきます。大きな産業構造の変化が起きていますし、場合によっては多くの雇用が失われる恐れもあります。
その中で、日本の製造業が目指すべき方向性とは何なのでしょうか?
私は3つあると思っています。
それは、
1.材料
2.中間材
3.生産財
です。
まず1.の材料についていえば、軽い自動車をつくるための高張力鋼板や、バッテリーをつくるためのフィルム等の材料(素材)、あるいは半導体材料などの高付加価値材料のことです。材料の開発は一朝一夕にできるものではなく、長い時間と歴史、また素材産業を支えるサプライチェーンがなければ不可能です。
また2.の中間材とは、例えば村田製作所が手掛けるセラミックコンデンサーや、ソニーが手掛けるCMOS画像センサー、あるいはボールネジやLMガイドといった製品や装置に組み込まれる部品のことです。
この中で、半導体や液晶パネル、あるいは太陽光パネルといった市場規模の大きな分野は中国などマス・プロダクション強国が優位性を持ちますが、電子部品や要素部品の様に多品種少量で顧客ごとのカスタマイズが求められる分野や、市場規模がそこまで大きくない分野は先進国に残ります。
さらに3.の生産財の特性として、種類は膨大ですが各分野の市場規模は小さいというロングテール構造であり、中堅・中小企業が有利な分野であるといえます。
ドイツは優良な中堅・中小企業が多く、また海外輸出比率が高いといわれていますが、その理由はドイツが生産財分野に強いからです。
逆に、東芝グループは超硬メーカーである東芝タンガロイを外資ファンドに売り、また日立グループも作業工具メーカーである日立工機を外資ファンドに売りましたが、東芝や日立の様な超大手グローバル企業からすると、切削工具や作業工具のマーケットは市場規模が小さすぎる、との判断で事業を手放しているのです。
経営を永続させるための鉄則は、「大きな海の小さな魚」になるのではなく、「小さな池の大きな魚」になることです。例えば一昨年のファクトリービジネス研究会の年末総会の特別ゲスト講師としてご講演いただいた静岡県の優良企業で東証一部上場のスター精密 佐藤会長は、「世界の市場規模が4000億円以上の分野には手を出さない」「小さなマーケットの中でシェア3割以上を獲得して価格決定権を得るのが鉄則」と言われていました。
ちなみに筆者は過去4回、ドイツで企業視察を行いましたが、ドイツが力を入れている分野も上記3分野です。
日本とドイツには次の様な共通点があります。
・英語圏(全世界で20億人)や中国語圏(全世界で15億人)といった大きな言語圏を持たない
・お隣の国、ポーランドはドイツの人件費の1/4であり、近隣国と価格勝負ができない
・第二次世界大戦の敗戦国であり、航空宇宙や軍事分野に手が出せない(長い間手が出せなかった)
この様に、今後、大きな産業構造の変化が起こったとしても先進国に残るであろう分野を見据えた上で、これから伸びる成長産業から仕事を取ってくるためのマーケティング戦略が求められると思います。
製造業・工場経営の最新ノウハウ資料を見る